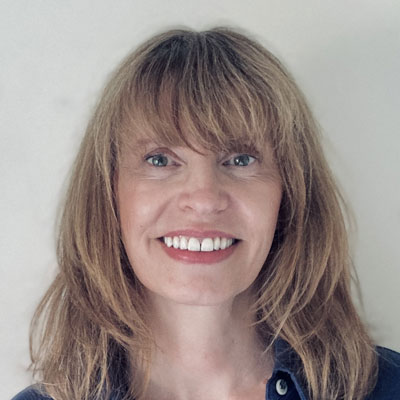
Shirley Harrison
SME Engagement Manager, AMRC
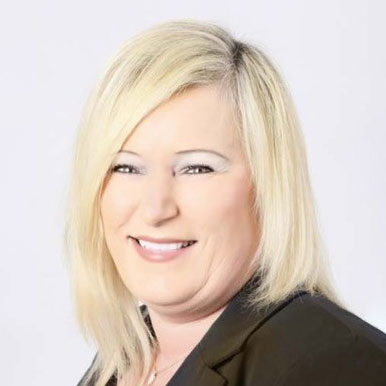
Melissa Conlon
Commercial Director, AMRC North West facility
A world-leading manufacturing research centre is helping small and medium enterprises through digital transformation and their journey towards net zero carbon emissions.
As SMEs prioritise rising costs and global competition, achieving net zero has become less prominent. However, industry experts recommend investing in technology and reviewing processes as a dual solution — benefiting both the company and the environment.
Manufacturing challenges in reaching net zero
The University of Sheffield Advanced Manufacturing Research Centre (AMRC), and its regional centres in Lancashire and north Wales, conduct research to de-risk and deliver practical industry applications. As part of the High Value Manufacturing Catapult, they also offer support in areas such as advanced connectivity; robotics and automation; and manufacturing information systems to firms big and small seeking expertise and advice.
AMRC SME engagement manager, Shirley Harrison, says: “Big issues for SMEs are attracting and retaining skilled staff, the cost of raw materials, energy bills and remaining globally competitive.” Other challenges include digital transformation, decarbonisation and supply chain resilience.
Helping SMEs with technology uptake
As a chartered mechanical engineer, Harrison guides small businesses with knowledge of emerging technologies and changing production techniques in manufacturing. “By adopting new technologies, businesses can help themselves become more competitive; they can automate processes and have less reliance on traditional manual processes and increase capacity,” she explains.
Advising on new, efficient techniques
In one example, process optimisation techniques were suggested to a SME whose precision engineered components were in particularly high demand. Before investing in new capital equipment, the firm wanted to explore the possibility of increasing capacity and reducing energy costs by using current facilities more effectively.
By taking a machining science approach, the centre was able to demonstrate to the SME how operational steps can be reduced from six to two — minimising the expensive and energy-intensive process.
After receiving support from the centre, the company said: “It was great to challenge our conventional wisdom of how we’ve always done things. The AMRC’s ideas have the potential to reduce production time from
two weeks to a matter of days, so we could offer reduced lead times when estimating for new business.”
Working with industry and academia, plus data scientists, the team aids firms in lowering emissions for net zero goals by analysing energy-use data. However, a recent British Business Bank survey found that 53% of SMEs were ‘not yet ready’ to prioritise decarbonisation.
For every pound invested in delivering
the project, £4.52 was generated.
Finding suitable sustainability strategies
The AMRC’s £20 million purpose-built Low Carbon Smart Building Demonstrator, based in its North West facility, is fitted with 25+ low carbon technologies that can be showcased to SMEs in a real-life demonstrator scenario. It also has a 10-step plan and funding to help companies decarbonise.
Commercial Director at AMRC North West, Professor Melissa Conlon, says: “We can help manufacturers to understand the impact of these low carbon technologies in their own facilities, and potentially adopt those that will make the biggest impact and assist with their journey to zero carbon manufacturing.”
The facility has specialist expertise in robotics automation and has a 5G Factory of the Future open-access testbed, which supports SMEs in digital manufacturing through the Rapid Digital Assist Programme (RADAR) project. It deals with firms on a commercial basis but, since 2019, has secured £9 million to work with 400+ Lancashire SMEs, primarily through the European Regional Development Fund (ERDF).
Benefits for businesses and local economies
An initial programme helped 207 Lancashire-based manufacturing SMEs adopt new technologies and processes with bespoke solutions. “An independent summative assessment calculated the net economic impact and concluded that, for every pound invested in delivering the project, £4.52 was generated,” says Conlon.
The programme supported 22 new businesses and 113 new-to-market products. It also created 156 new jobs with a net economic impact of £23.5 million. A second two-year programme supported 201 manufacturers — creating 236 jobs and generating £15.90 for the local economy from every £1 invested.
One company receiving RADAR support described it as a ‘game-changer’ for their business, saying it is “providing invaluable access to software engineers and cutting-edge technologies that were previously beyond our reach as a small company.”