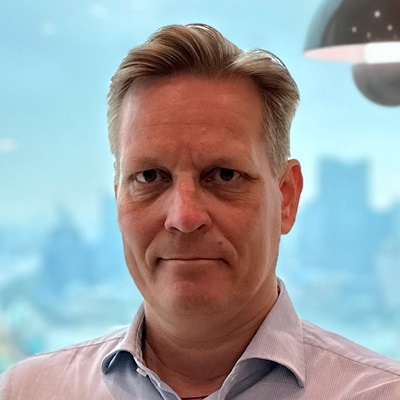
Saku Järvinen
Business Development Director, Visual Components
There are approximately 1.5 million industrial robots on the planet, manually programmed to complete tasks in the manufacturing environment. That phenomenal amount of machinery requires human expertise to successfully weld, paint or even assemble products.
Manual programming takes time. Weeks can go by where a robot is being taught how to complete a process before it can offer any value. To future-proof their operations, manufacturers need to explore automation that places humans at its heart.
Human-centric automation can address skills shortages
Automation is inevitably making its way into the manufacturing environment. In addition to lost efficiencies and accumulated costs, manual robot programming is a strain on hard-to-source human resources and often unsafe. Approximately 10 million manufacturing jobs globally remain unfilled due to the skills gap, which adds to the time taken to prepare robots to complete tasks.
Where heavy machinery requires human input, employees are frequently needing to climb ladders and position themselves in potentially dangerous settings. A wide range of automation technologies are also coming into play, such as new robot brands, complementary technologies (e.g. laser tracking) and different software solutions, which can further complicate processes on the manufacturing floor and add to the human workload.
Automation of robotic programming is the answer. Efficient programming of a new or existing robot work cell can be achieved by offline programming software (OLP). Rather than force workers to test and train robotic applications in the real world, OLP software uses a virtual model of the robot and work cell and accurately simulates its processes and workflows, allowing engineers to evaluate trade-offs and make more efficient and cost-effective decisions.
Human-centric automation will become the norm as robot brands continue to proliferate.
Benefits of offline programming software
Automation of robot programming with OLP software can provide higher and repeatable levels of quality compared to manual programming. There’s little room for error due to established accuracy and consistency that’s stored in the software, rather than in the brains of professionals who may fail to share this knowledge or leave the business before getting the opportunity to do so.
A crucial benefit — one that is commonly overlooked — is that it can validate a design for manufacturing. If a deployment isn’t tested in a virtual environment, it’s all too easy to make a simple and costly mistake, such as the robot not being able to reach a critical position.
Simple. Visual. Powerful. Design and validate new production solutions confidently.
Unlimited opportunities to make mistakes in a virtual sandbox means that a process can be refined to the finest detail before being deployed in the real world. With OLP, organisations have been able to reduce manual programming human work hours by 80%, bring down programming time by 60% and improve production lead times by 62%.
Programming can also happen concurrently alongside robot deployment, as opposed to sequentially. This allows for much less time spent on preparation before launching a new product into production. Because it’s all completed offline and away from the physical machinery, there’s a reduced risk of accidents and injuries.
The human factor in robotic deployment
People fear that as robots become more widely deployed and provide optimum value on the factory floor, humans will be pushed aside. However, process knowledge is still needed. It’s up to the younger generation, who are versed in the use of applications and virtual 3D environments, to work with OLP solutions to support automation.
To further feed that pipeline of talent to utilise such platforms, we need to see more examples of the technology being used at the educational level to train students before they enter the workplace. Over the next 10 to 15 years, the manufacturing sector will demand more and improved OLP solutions to make the most of their robotic investments as technology improves.
Human-centric automation will become the norm as robot brands continue to proliferate. While manual programming processes still exist today, they will soon be considered a relic of the past.