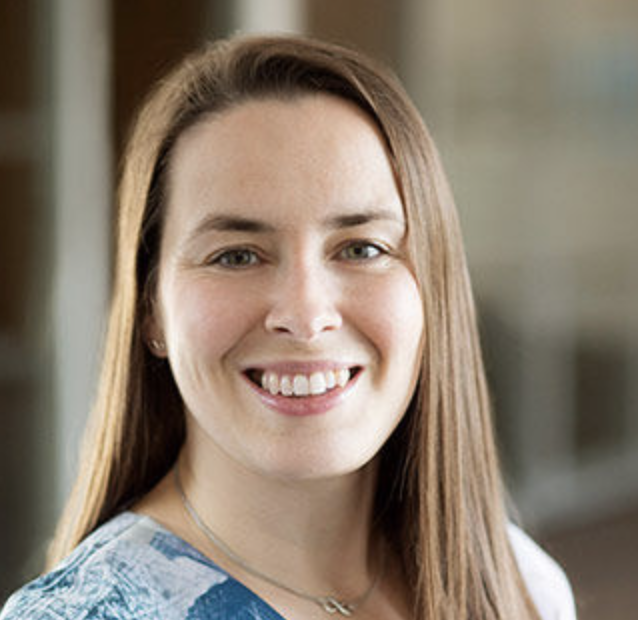
Cara Haffrey
Industrial Manufacturing and Automotive leader at PwC.
UK manufacturing is operating in a more complex environment than ever before, says Cara Haffey the Industrial Manufacturing and Automotive leader at PwC.
Whether it’s further advances in automation and the impact of AI, the move towards connected factories and digitalisation of the supply chain or the disruption caused by the rapidly developing way of doing business, manufacturers face an increasing number of decisions regarding investment and innovation.
Uncertainty over the outcome of the Brexit negotiations is already impacting talent, supply chain, raw material costs and exports. At the same time however, November’s PMI figures were very positive. Meanwhile, customers are also facing seismic changes in their sectors including further industry convergence.
Uncertainty over the outcome of the Brexit negotiations is already impacting talent, supply chain, raw material costs and exports.
All this is against a backdrop where labour productivity in services grew by 0.2% in the last quarter while manufacturing fell by 1.3% – something the UK Government is hoping to redress through its Industrial Strategy. This long-term blueprint for action aims to see the UK become a front-runner in the fourth industrial revolution (41R)
The Government has already highlighted the leading role the UK can play in connected, autonomous vehicles and clean energy technology where city and off-road ‘test-beds’ across the country are already helping to accelerate these into practical application. This will be further boosted by a new £2.3bn investment fund for research and development.
We predict that electric vehicles will become cheaper to run than petrol or diesel models, when you factor in traditional costs such as depreciation, fuel, servicing, taxes and insurance. Our latest Connected Car research into those with mobility challenges revealed that six in 10 (57%) believe connected and autonomous vehicles will improve their quality of life as well as educational and employment prospects. The question is: who will adopt and apply these en mass first – fleets, last mile journeys, freight transport, or specific “smart” cities? Whatever the answer, the UK wants to be in the driving seat.
Driving the digital revolution
But what about the wider implications for manufacturers? Industry 4.0, is characterised by the increasing digitisation and interconnection of products, value chains and business models – supported and enabled by technologies including the Industrial Internet of Things (IIoT), artificial intelligence (AI), advanced robotics, machine learning and billions of connected devices and sensors.
In the longer-term manufacturers will see an evolution in their relationship with their customers.
As the supply chain becomes digitalised this will help to support more efficient, more agile and more responsive supply chains. With increasing numbers of sensors, connected objects and therefore data, manufacturers must look at their data analytics, IT infrastructure, and cyber security. The conversation on cyber security must move from not only protecting employee data, customer data and financial data and intellectual property to the threat of hacking physical processes in manufacturing and connected products such as the car. And manufacturers must look at every part of their supply chain when addressing this – you are only as strong as your weakest link.
In the longer-term manufacturers will see an evolution in their value chains and relationship with their customer. While Industry 4.0 is predominantly about leaner processes, efficiencies and cost cutting, in the future it will be about generating new forms of revenue. Efficiencies from predictive maintenance will be a benefit for their customers as much as for themselves. What’s more disruption and competition could come from outside their sectors from more agile companies as the barriers to entry lower as technologies become cheaper. Manufacturers will need to fundamentally review their business models – and they may even need to look at new partnerships in order to capitalise on innovation.
Meanwhile, investment in physical and digital infrastructure as well as collaboration between business, government and universities is needed to convert innovation into new products and services, unlock the skills challenge and drive prosperity and productivity. And regions must identify how they will play in the 4th industrial revolution. What will they be famous for and how will they achieve this?
Powering your pipeline
Beyond attracting talent, manufacturers also have a significant role to play in transforming skills and even their organisational culture. Fears that robotics and AI will destroy roles, and change others so radically that the existing workforce won’t be able or willing to do them, abound. But the implications are certainly profound reaching much further and wider across the workforce as new value chains and business models develop, tackling a more digital environment and advances in cobotics – even creating new roles.
While STEM skills remain critical, manufacturers also need to recruit people with soft skills and an understanding of what their customers want.
Employers are already looking for new and emerging skills, which is why we have launched our own new technology degree apprenticeships with the Universities of Birmingham, Leeds and most recently, Queen’s University Belfast. The UK’s catapult centres are also great examples in bringing industry and talent together and there are several individual examples of manufacturers driving training of STEM skills.
While STEM skills remain critical, today’s CEOs also need to recruit people with softer skills such as empathy and an understanding of what their customers and ultimately the consumer is trying to achieve. Interestingly, four in five CEOs in our CEO survey expressed challenges in attracting people talented in creativity and innovation or leadership, with emotional intelligence (70%), problem-solving (69%), and adaptability (68%) also an issue.
Only with this variety of skilled talent on board will they be able to build the customer relationships needed to sell complex, multifaceted solutions, and then collaborate with those customers to run the solutions and embed them in their businesses. Those with relevant industry and sector experience will be as important as engineers and technologists. Competition for talent will be fierce, coming from outside the sector. Companies will need to build a culture of innovation that both attracts new and develops existing talent and digital skills.
I believe the United Kingdom can take advantage of its apparent lack of remaining heavy industrial legacy to build a brand around the technology of tomorrow. In fact it is the manufacturing industry that has driven much of the technologies of today. To succeed we must work together, whether on smarter cleaner transport, the future of our cities or educating the future talent pipeline. Most of all we must enable and empower the workforce and future talent pipeline to harness the opportunities of 4IR.